- Home
- Main Catalog
- Buffer layers - Build up - Cladding - Joining
- Dissimilar & stainless steels
- Nicrolloy 29.9
Nicrolloy 29.9
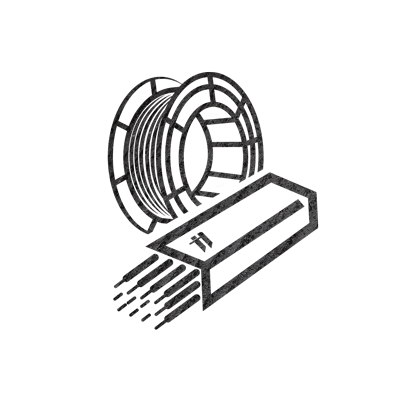
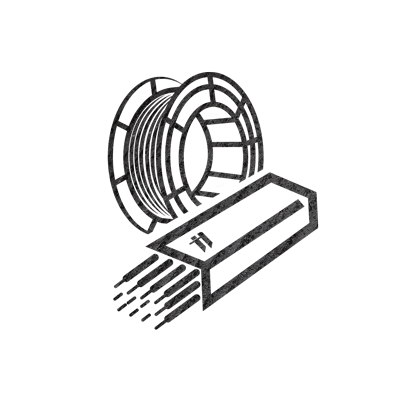
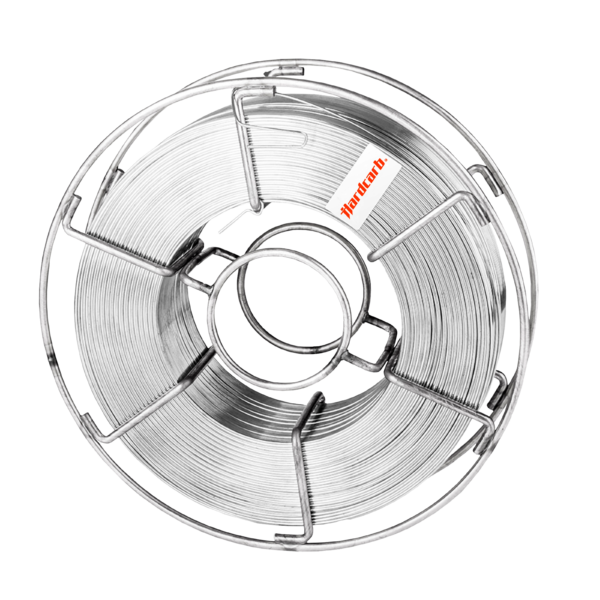
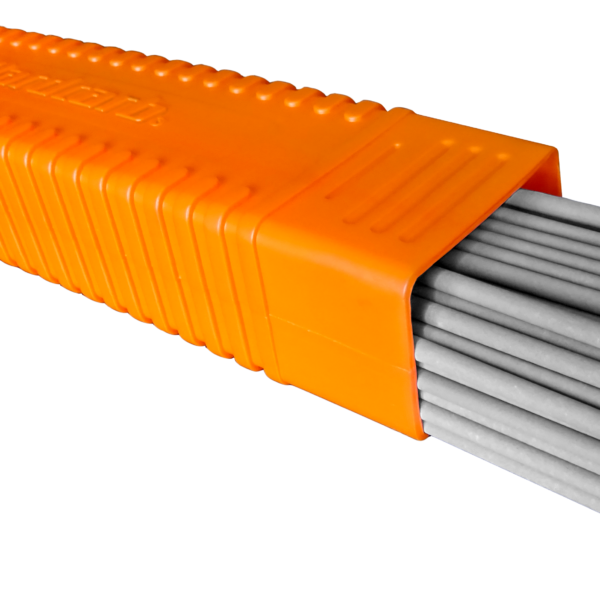
Specially formulated austenitic-ferritic stainless steel welding deposit (high ferrite content) for welding “difficult-to-weld” and dissimilar steels which need high integrity, safety, and welder-friendly usability. The weld metal remains ferritic, even after dilution with an austenitic base metal forming elements such as Mn, Ni und C and is thus highly crack resistant. Produces plastic weld metal of high tensile strength, impact proof, tough, and acid and heat resistant up to 1,000° C.
Weld deposit characteristics:
Duplex austenite-ferrite microstructure with about 40% ferrite. Combination of high alloy and high ferrite content gives extreme tolerance to dilution on a wide range of hardenable and alloy steels with minimum or no preheat. Weld deposit work-hardens and gives good wear and friction resistance. Useful for resistance to corrosion and to high temperature scaling up to about 1000°C, but not recommended for structural applications above 300°C or for welds to be post-weld heat treated, owing to embrittlement.
Recommended uses and applications
» for joining difficult-to-weld base materials such as: highcarbon steel, tool steel, spring steel, manganese steel, casehardening steel, high-speed steels, cast steels, screening steels.
» for joining above materials to other dissimilar steels.
» for surfacing and repair welding rails, shafts, couplings, impellers, hot work tools, pressing and trimming tools, as well as stamping dies
Additional info
Anti-wear suitability
Metal-to-Metal friction Metal surfaces in relative motion forced into contact with or without lubricant. Degradation by the formation of micro-welds between the contacting surfaces. | - |
High pressure abrasion Wear by relative movement under pressure of mineral particles of suitable hardness, shape and texture to remove material from the metal surface, leaving superficial deformation. | - |
Cavitation Tearing out of grains from the metal surface by the formation and implosion of bubbles in a liquid in rapid motion. | - |
Mechanical fatigue Fatigue and formation of cracks in surface regions due to tribological stress cycles that result in the separation of material. | - |
Thermal fatigue Cyclic exposure to high temperatures leading to permanent deformation by alternate expansion and contraction. Alteration of the structure and properties of the material. | - |
Hot oxidation Creation of a poorly adhering oxide layer that reforms constantly. Degradation by loss of material thickness. | - |
Workability
Work hardening Work hardening is the process of making a metal harder and stronger through plastic deformation. When a metal is plastically deformed, dislocations move and additional dislocations are generated. | |
Edge retention Suitability for creating sharp edges and retaining them during operation. | |
Machining Machinability is the ease with which a metal can be cut (machined) permitting the removal of the material with a satisfactory finish at low cost. | Highly suitable. |
Mechanical properties
Yield strength | > 500 Mpa |
Tensile strength | 700 - 800 Mpa |
Elongation A5 | 20% |
Impact strength | > 30 J (+20°C) |