Nicrolloy 250
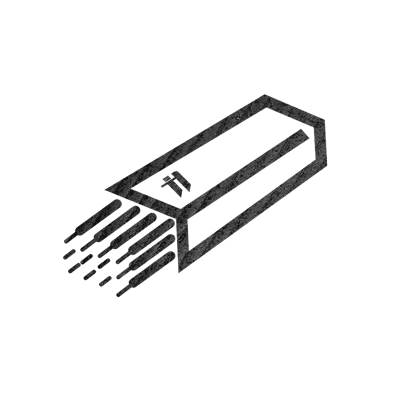
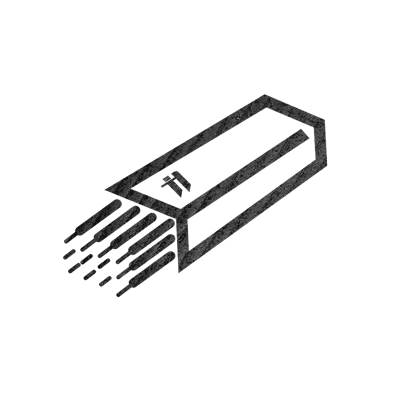
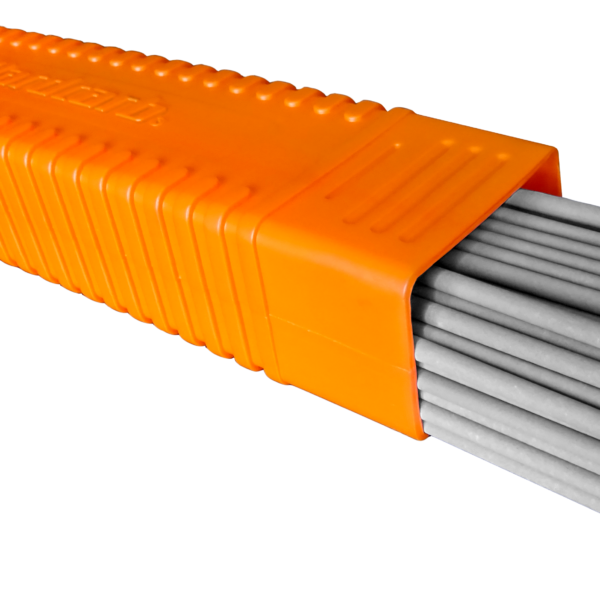
A special graphite coated electrode with a NiCu-alloyed core wire suitable for safe cold welding of grey cast iron, cast steel and malleable cast iron. Due to a nearly colour matching deposit and its good welding properties this electrode is suited especially for repairing casting or machining defects on new castings. The electrode is well suited for the joining of cast iron pieces to monel alloys, stainless and ordinary steels.
Weld deposit characteristics:
The weld metal produces nickel-copper deposits which are extremely shallow yet with sufficient depth of fusion, ensuring minimum dilution of the weld metal by the base metal. The heat effected zone is very narrow.
This electrode excels by very high crack-resistance and high tensile strength of the weld metal. It produces quietly and intensely flowing weld metal with very little spattering and easily removable slag. Filler metal has the same colour with that of the work piece and the porosity-free deposits can easily be machined.
Recommended uses and applications
» for safe cold welding and repairing of grey cast iron, cast steel and malleable cast iron.
» for repairing casting or machining defects on new castings.
» for re-building worn surfaces.
» for the joining of cast iron pieces to monel alloys, stainless and ordinary steels.
» for broken casting repairs.
» to produce Ni-Cu corrosion resistant layer by cladding ordinary cast iron parts.
Additional info
Anti-wear suitability
Metal-to-Metal friction Metal surfaces in relative motion forced into contact with or without lubricant. Degradation by the formation of micro-welds between the contacting surfaces. | - |
High pressure abrasion Wear by relative movement under pressure of mineral particles of suitable hardness, shape and texture to remove material from the metal surface, leaving superficial deformation. | - |
Cavitation Tearing out of grains from the metal surface by the formation and implosion of bubbles in a liquid in rapid motion. | - |
Mechanical fatigue Fatigue and formation of cracks in surface regions due to tribological stress cycles that result in the separation of material. | - |
Thermal fatigue Cyclic exposure to high temperatures leading to permanent deformation by alternate expansion and contraction. Alteration of the structure and properties of the material. | - |
Hot oxidation Creation of a poorly adhering oxide layer that reforms constantly. Degradation by loss of material thickness. | - |
Workability
Work hardening Work hardening is the process of making a metal harder and stronger through plastic deformation. When a metal is plastically deformed, dislocations move and additional dislocations are generated. | |
Edge retention Suitability for creating sharp edges and retaining them during operation. | |
Machining Machinability is the ease with which a metal can be cut (machined) permitting the removal of the material with a satisfactory finish at low cost. | Highly suitable. |
Mechanical properties
Yield strength | > 250 Mpa |
Tensile strength | > 400 Mpa |
Elongation A5 | > 15% |
Impact strength | - |