- Home
- Main Catalog
- Buffer layers - Build up - Cladding - Joining
- Dissimilar & stainless steels
- Nicrolloy 13.04
Nicrolloy 13.04
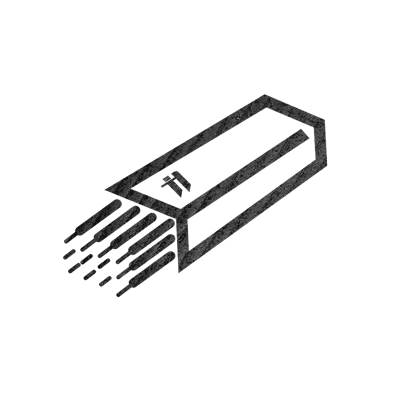
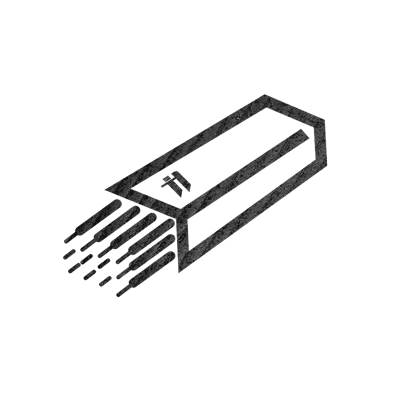
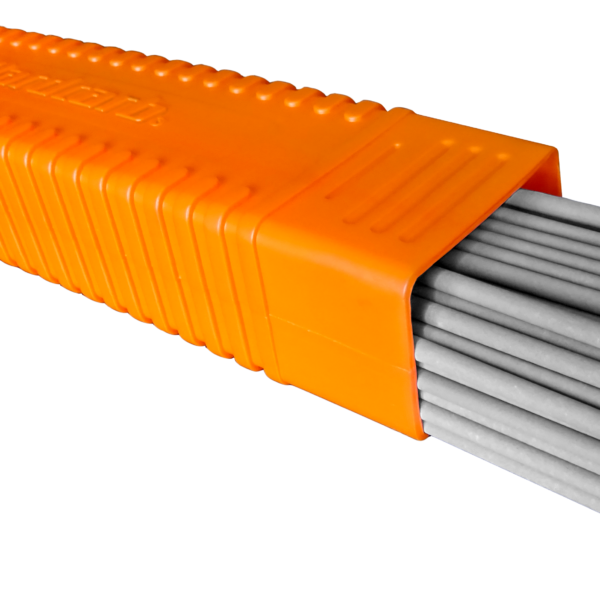
A high strength (>700MPa) air-hardened martensitic stainless steel electrode with good resistance to corrosion, hydro-cavitation, sulfide stress cracking, and good sub-zero toughness. The alloy is highly suitable for welding on tough, corrosion resistant continuous-cast rolls and also to overlay mild and low alloy steels subjected to wear.
Weld deposit characteristics:
The weld deposit is an air hardened martensitic stainless steel that requires preheat and post-weld heat treatment to achieve welds of adequate ductility for many engineering applications. In the PWHT condition the microstructure consists of tempered martensite with some retained austenite. Due to an optimum balance of alloying components the weld deposit yields very good ductility, toughness and cracking resistance despite of its high strength.
Recommended uses and applications
» for welding AISI 410 and AISI 420 types of stainless steel.
» for construction of hydro turbines, compressors and other parts subjected to corrosion from water, steam and sea water atmosphere.
» for surfacing of carbon steel and low-alloy steel to resist heat, corrosion, erosion and abrasion.
Additional info
Anti-wear suitability
Metal-to-Metal friction Metal surfaces in relative motion forced into contact with or without lubricant. Degradation by the formation of micro-welds between the contacting surfaces. | - |
High pressure abrasion Wear by relative movement under pressure of mineral particles of suitable hardness, shape and texture to remove material from the metal surface, leaving superficial deformation. | - |
Cavitation Tearing out of grains from the metal surface by the formation and implosion of bubbles in a liquid in rapid motion. | - |
Mechanical fatigue Fatigue and formation of cracks in surface regions due to tribological stress cycles that result in the separation of material. | - |
Thermal fatigue Cyclic exposure to high temperatures leading to permanent deformation by alternate expansion and contraction. Alteration of the structure and properties of the material. | - |
Hot oxidation Creation of a poorly adhering oxide layer that reforms constantly. Degradation by loss of material thickness. | - |
Workability
Work hardening Work hardening is the process of making a metal harder and stronger through plastic deformation. When a metal is plastically deformed, dislocations move and additional dislocations are generated. | |
Edge retention Suitability for creating sharp edges and retaining them during operation. | |
Machining Machinability is the ease with which a metal can be cut (machined) permitting the removal of the material with a satisfactory finish at low cost. | Highly suitable. |
Mechanical properties
Yield strength | > 700 Mpa |
Tensile strength | > 850 Mpa |
Elongation A5 | 15% |
Impact strength | > 40 J (+20°C) |